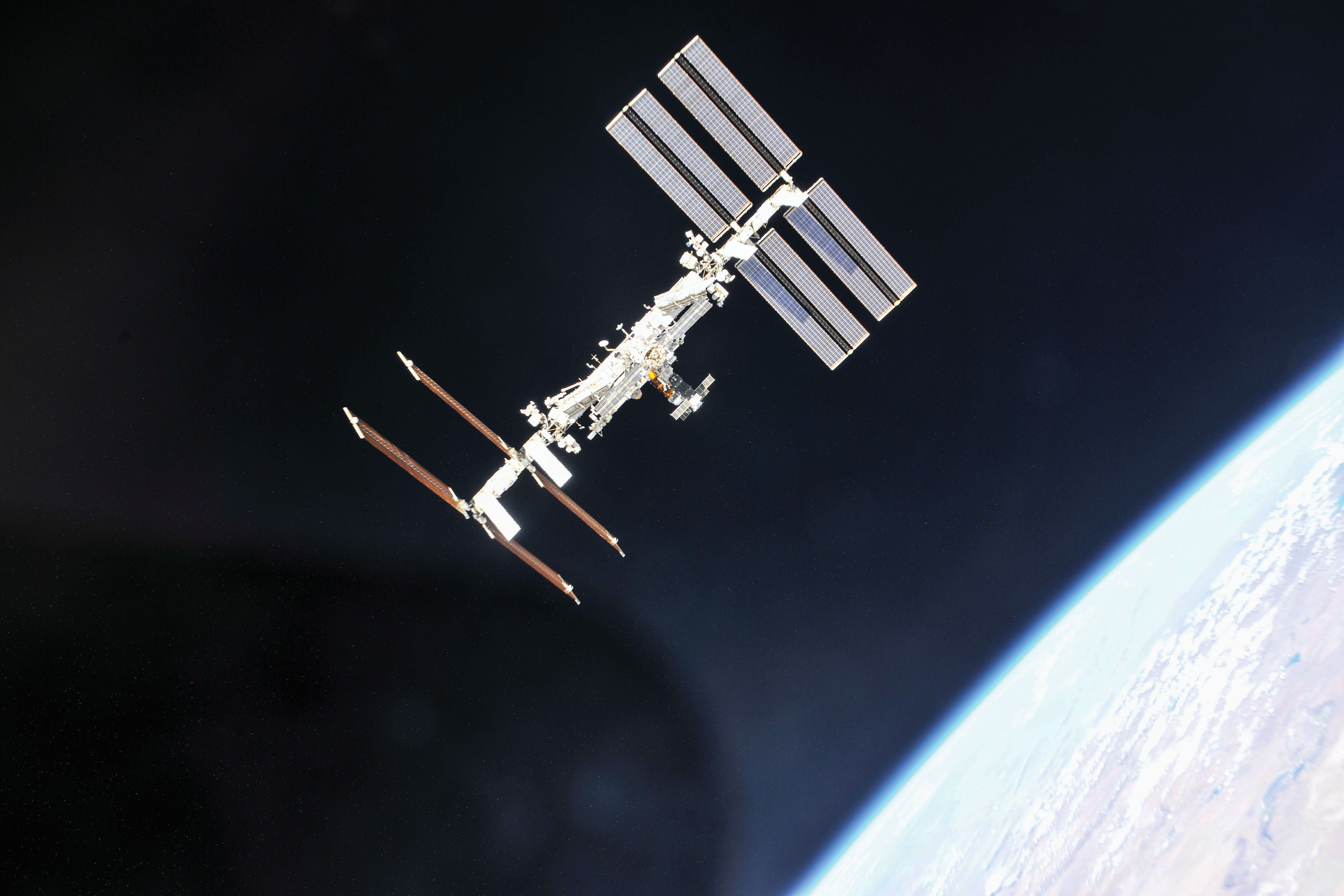
There’s No Place Like Space
Arthur Paolella is studying which 3D-printed materials can survive the harsh environment of space. What he learns could advance satellite technology.
Like many people of his generation, Arthur Paolella ’82 recalls being mesmerized while watching the Apollo 11 moon landing unfold on live TV. The sight of Neil Armstrong taking those first steps on the lunar surface helped instill what would become a lifelong desire to work in the space industry.
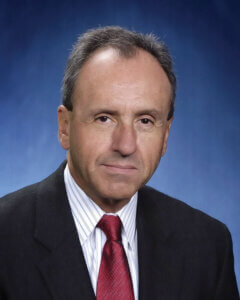
Arthur Paolella’s work involves testing how 3D-printed materials perform in low Earth orbit on the International Space Station.
Now that dream has become reality. As a senior scientist at L3Harris Technologies, an aerospace and defense technology company based in Florida, Paolella oversees research and development of 3D-printing for manufacturing communications satellites. The hope is that the use of robust 3D-printed materials will translate to building more cost-effective, lightweight, and long-lasting satellites.
Recently, Paolella’s main experiment, which focuses on whether and how 3D-printed materials survive the harsh environment of space, was aboard the International Space Station (ISS). Last year, he and his colleagues attached samples of various materials to a rocket that docked with the ISS. The samples were scheduled to come back to Earth in December (after this magazine went to print) for extensive testing.
“In recent years, 3D printing has become very popular in developing a number of things, particularly modeling and prototype forms. But I wanted to see how the technique would work for a communications system in space,” says Paolella, who received his undergraduate degree in electrical engineering from Monmouth and a doctorate in electrical engineering from Drexel University. “The space environment is very brutal. There’s radiation, huge temperature extremes, and, in some cases, orbital debris such as micrometeorites.”
The ISS circles the Earth every 90 minutes, roughly, meaning that the samples went from sunlight to darkness multiple times per day. On top of this temperature fluctuation, they were also exposed to atomic oxygen in space. This elemental form of oxygen doesn’t exist naturally for very long on the surface of the Earth but is abundant in low Earth orbit. Atomic oxygen reacts with other materials very easily, exposing satellites to damaging corrosion.
Assuming that some of the samples endure, L3Harris plans to incorporate those 3D-printed materials into new satellite designs. The company’s diverse customer base uses satellite technology for applications like communications, imaging, and weather. In addition, 3D printing could allow for manufacturing on an as-needed basis in space—for example, if an antenna or radio is damaged, a 3D printer on the ISS could quickly create a replacement.
“As a kid, even at the age of 5 or 6, I had a curiosity with electronics. I took everything apart—anything that had electronics in it, I would just take it apart to see how it worked,” says Paolella. “That’s why I went into electrical engineering at Monmouth, because that was an interest that I always had, and then I eventually circled back into my fascination with space.”